What do you want from your BMS. Part 2: Condenser Coils
What do you want from your BMS. Part 2: Condenser Coils
Follow the link below to read part 1 that first appeared on LinkedIn:
What do you want from your BMS?
Before I answer the question, let’s look at the diagram below that many of us are familiar.
Point A: The R22 vapour, superheat to about 70°C, leaves the compressor discharge and enters the condenser at a pressure of about 14 bar.
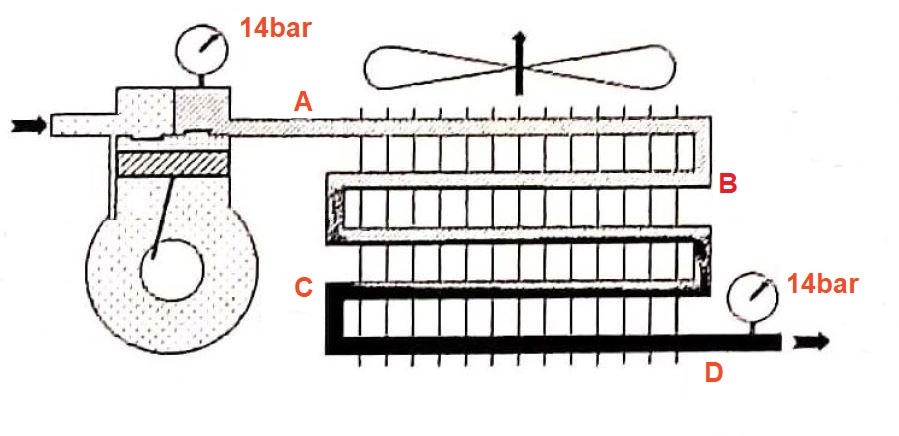
Between A and B: The vapour de-superheats at a constant pressure.
Point B: The first droplets of liquid R22 appear. The temperature is 38°C, and the pressure is still around 14 bar
Between B and C: The vapour continues to condense. There are more and more liquid present and less and less vapour.
The pressure and the temperature are constant (at about 14 bar and 38°C respectively) per the pressure-temperature relationship of R22.
Point C: The last vapour molecule condenses at 38°C, and there is therefore only liquid present. The temperature and the pressure remain constant at about 38°C und 14 bar respectively.
Between C and D: As all the R22 condensed. The liquid refrigerant continues to cool since it is in contact with the air over the condenser.
Point D: At the condenser outlet, there is only liquid R22 present. The pressure is still at 14 bar, but the temperature of the liquid has fallen to around 32°C.
We can represent the changes taking place in the R22 as follows:
From A to B: desuperheating of vapour from 70°C to 38°C, where A-B is the desuperheating zone of the condenser.
At point B: the first drop of liquid appears.
From B to C: Condensation of the R22 at 38°C and 14 bar. B-C is the condensation zone of the condenser.
At point C: the last molecule of the vapour condenses.
From C to D: Sub-cooling of the liquid R22 from 38°C to 32°C, C-D is the sub-cooling zone of the condenser.
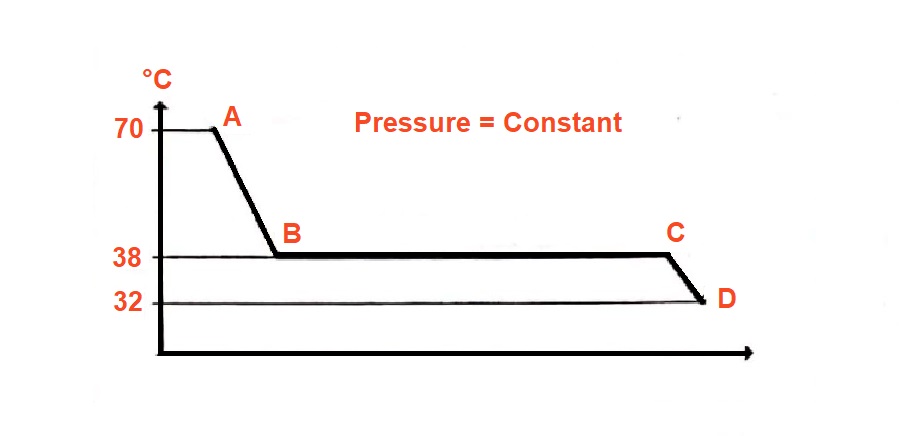
Throughout all this, the pressure has remained constant at the reading shown by the HP gauge at 14 bar.
Now let’s take a look at what happened on the airside:
The external air arrives at the condenser at 25°C and is heated to 31°C by absorbing heat that is released from the refrigerant.
We can represent the changes that have taken place on the airside of the condenser and the resulting condensation temperature graph below.
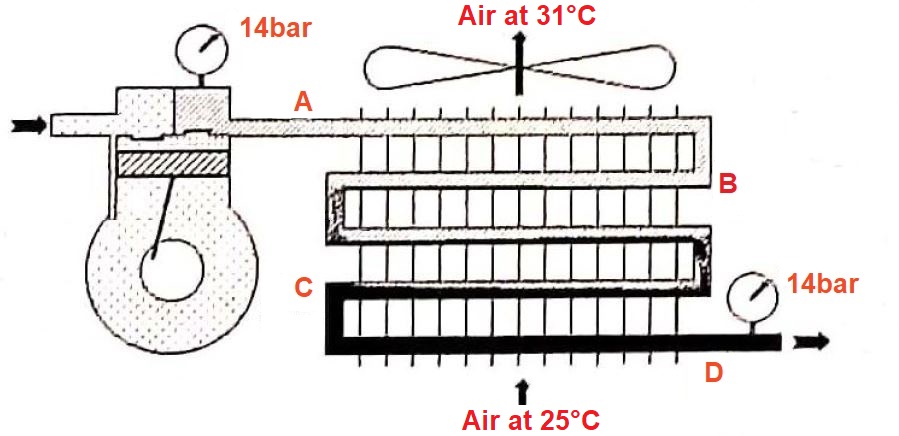
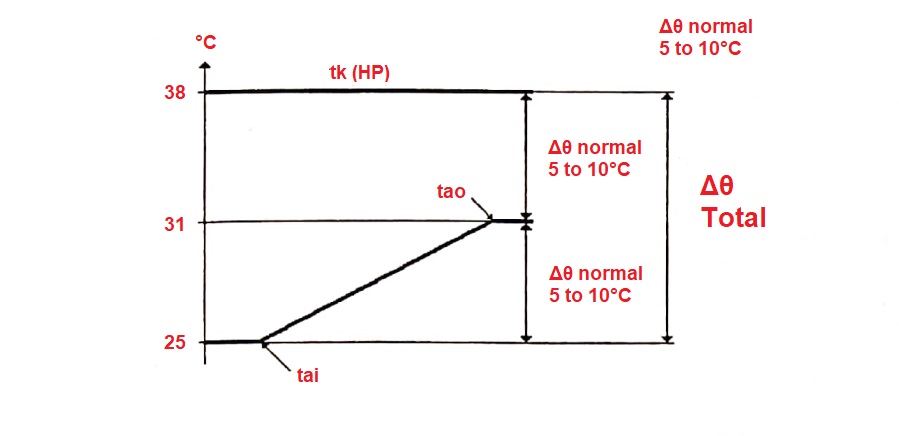
tai: temperature of the air at the condenser inlet
tao: temperature of the air at the condenser outlet
tk: condensation temperature, as read on the HP gauge
Δθ: represents the difference between two temperatures.
Similarly, the Δθ between the condensation temperature and the air temperature at the outlet of the condenser is also about 5K to 10K, which in the case above 7K.
Hence the Δθ total (tk–tai) can be between 10K to 20K, which is generally around 15K and the case above being 13K.
Why is Δθ important for a given condenser? It is because Δθ total remains approximately constant for a given condenser.
By using the value in the example above, i.e. 13K, we can quite safely say that for an external temperature (tai) of 30°C, the tk should be equal to about 43°C.
ie tai + Δθ total ~ 30°C + 13K = 43°C
Which would mean an HP shown on the gauge of about 15.5 bar for R22, 10.1 bar for R134a and 15.8 bar for R404A.
So how is the above relevant for BMS to enable predictive maintenance capabilities. We can start trending the calculated tai + Δθ total against the measured pressure, hence tk; the higher the deviation will indicate that something is amiss and warrant an alarm. It’s important to note it’s the anomaly that we always look for in the trends in predictive maintenance. The trend is your friend!
Before I sign off for now, here is a parting question; can we expect the BMS contractor to know the above? We will surely need to discuss and impart what we want for them to implement. It’s only fair.
Read What do you want from your BMS on direct expansion evaporators.
Related
Read more: Fan wall
Read more: How to verify the percentage of outside air in an enclosure
Read more: BCA Part J5 Air-conditioning system control
Read more: Microbial Induced Corrosion (MIC) in Pipes
Read more: Is your kitchen exhaust system a fire hazard
Read more: What is coanda effect